Digital Mapping
Digital profile mapping enhances precision and efficiency in inspection, alignment, and maintenance tasks across various industrial applications.
Areas of Application
- Leveling and Catenary Measurement
- Assessment of shaft alignment against OEM’s catenary design.
- Coupling / Shaft Alignment Checks (End-to-End)
- Compare shaft positions to design specifications.
- Shaft center location at each bearing without requiring rotation.
- Permanent alignment history for wear monitoring.
- Turbine Alignment and Inspection
- Steam Path / Bore Alignment: HP, IP, and LP sections.
- Coupling Face Runout: Measuring rotational inconsistencies.
- Ovality: Turbine casing shape verification.
- HP Inner Casing and Barrel Centering: Ensures proper fit and alignment.
- Inspection and Calibration
- Robot calibration.
- Tool building and setup.
- Squat/load checks under hot and cold conditions.
- LP bore alignment for blade rings/diaphragms.
Key Features and Processes
- Efficient and Accurate Inspections
- Complete coupling/shaft alignment inspection in ~8 hours.
- Minimal setup and fewer instrument adjustments.
- Couplings remain bolted, reducing labor-intensive rim and face checks.
- Advanced Data Processing
- Easy data analysis and historical comparison.
- Permanent records allow wear and movement monitoring over decades.
- Precise location recording for future reference.
- Versatile Tools and Techniques
- Probes for inspecting steam unit components like blade rings/diaphragms.
- Enhanced accessibility to difficult-to-reach areas.
Advantages
- Efficiency: Reduces time for alignment and inspections.
- Cost Savings: Minimizes downtime and heavy component handling.
- Ease of Use: Simplifies data correlation and recall.
- Improved Accuracy: Enhanced precision for alignment and symmetry checks.
- Time Savings: Saves productive days in turbine overhauls, maintenance, and installations.
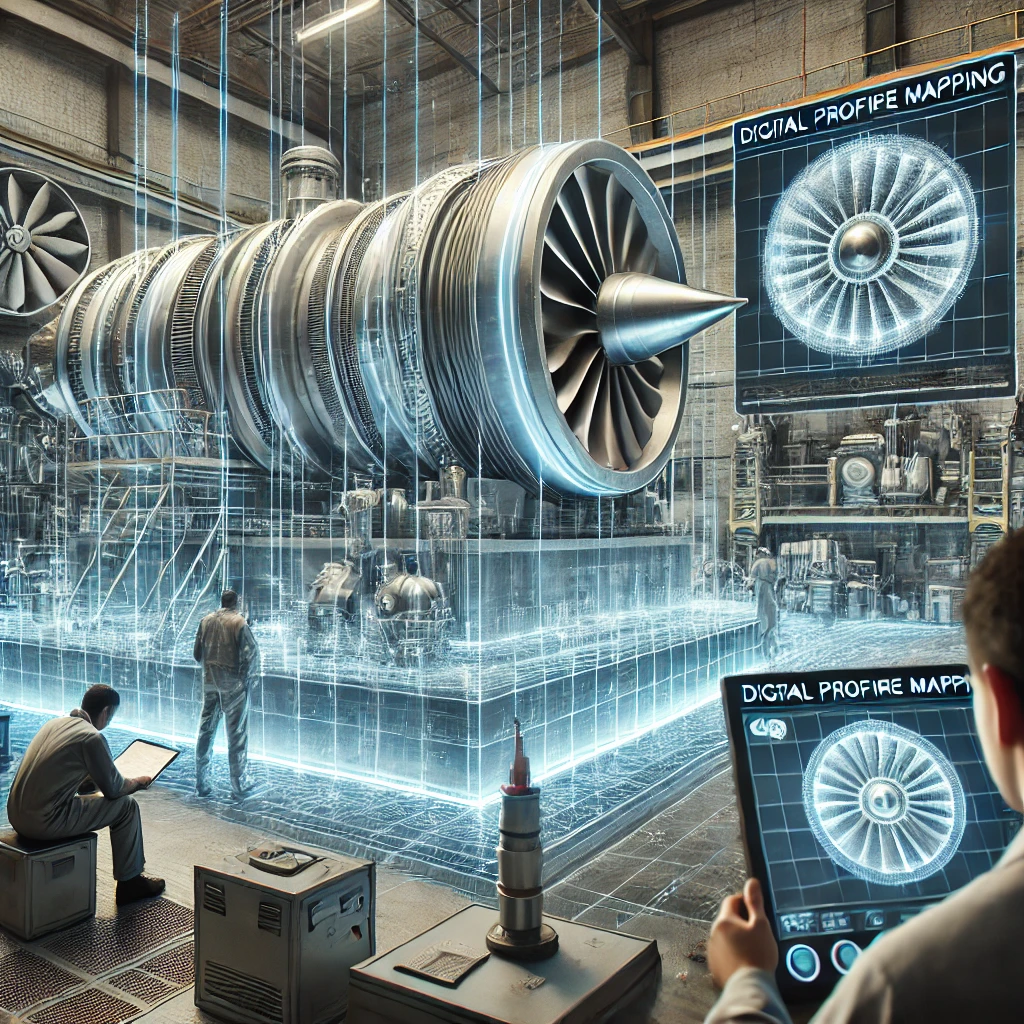